
0. 引言
煤矿辅助运输系统是煤矿日常生产经营的重要组成部分,除煤炭运输外,人员、材料、设备、物资等都通过辅助运输系统进行运送。辅助运输分为有轨电车、无轨胶轮车辅助运输,无轨胶轮车辅助运输具有机动、灵活、效率高等优势,陕北地区尤为适用。随着辅助运输车辆的增多和相关技术的发展,对井下辅助运输自动驾驶车辆的需求也逐渐增多[1-5]。车辆自动驾驶系统主要包含环境感知系统、车辆定位系统、车辆决策系统及车辆控制系统4个部分[6-9],其中车辆定位系统是车辆自动驾驶系统的关键系统之一,由车辆定位系统获取车辆实时位置,以控制车辆按照合理路线行驶。煤矿辅助运输车辆大多采用无线定位方式,普遍动态定位精度为3 m以上,不能满足煤矿自动驾驶定位精度的需求,且实时车辆定位数据发送到地面上位机,由上位机进行判断分析后通过矿井网络再下发至辅助运输车辆,该过程耗时约400 ms以上,不能满足自动驾驶车辆对定位信息实时获取的需求[10-11]。因此,实现煤矿车辆精准定位对井下辅助运输自动驾驶具有重要意义。通过查阅大量参考文献,发现目前对车辆定位的相关研究主要集中在地面和露天等场景[12-13] ,并以GPS定位为主。但煤矿井下巷道没有GPS定位信号,且煤矿井下巷道环境条件比地面场景更复杂、恶劣。
针对上述问题,本文提出了一种煤矿自动驾驶磁寻迹定位技术。通过在井下巷道布置具有ID编号的无源感应磁钉,在辅助运输车辆上安装磁感应天线,当装有磁感应天线的车辆经过巷道中预先布置的无源感应磁钉时,磁感应天线的磁场将产生脉冲信号,实时获取该脉冲信号在磁感应天线磁场范围内的具体位置,计算出车辆所在巷道位置和行驶路线中心的偏差位置,从而达到定位寻迹的目的。
1. 磁寻迹定位技术原理
通过在煤矿巷道适当位置布置磁钉,在车辆合适位置安装磁感应天线装置,磁感应天线下方区域持续发送具有传输频率的能量场,当磁感应天线经过磁钉时,磁钉受磁感应天线磁场的作用产生脉冲信号,该脉冲信号将对天线持续输出的能量场,产生脉冲式能量变化,磁感应天线实时感知能量场脉冲式能量变化,根据该变化来判断磁钉所在能量场范围内的具体位置,磁感应天线产生能量场的范围是已知的,通过磁钉和磁感应天线中心点的相对位置可判断出磁感应天线中心点所处的巷道位置,磁钉所在巷道的位置已提前布置。磁感应天线将定位信息通过CAN总线通信接口转发给车辆控制系统,控制系统根据磁感应天线中心点与磁钉的相对位置,计算出车辆所在巷道位置和行驶路线中心点的偏差位置,从而达到定位寻迹的目的。磁寻迹定位技术原理如图1所示,图中X和Y分别为车辆行驶横向和纵向距离,△X为磁感应天线距磁钉的距离。

2. 磁寻迹定位流程
煤矿自动驾驶车辆磁寻迹定位流程如图2所示。操作人员通过上位机软件或车辆启动按钮启动车辆,车辆启动后供电系统给磁感应天线上电进行程序初始化,当初始化完成且自动驾驶系统完成自检,车辆开始运行自动驾驶程序,当安装有磁感应天线的自动驾驶车辆经过预先布置在行驶路线的磁钉时,磁感应天线根据磁感应脉冲信号获取磁钉所在位置信息及编码数据,通过磁寻迹定位技术相关算法计算车辆当前行驶位置,判断数据是否异常,若数据异常重新进行数据获取和判断,否则将定位信息推送给车辆控制系统。车辆控制系统根据定位信息控制车辆继续进行自动驾驶,如系统判断当前位置未到达车辆行驶终点,控制车辆继续进行自动驾驶过程,否则自动停车,完成本次自动驾驶。
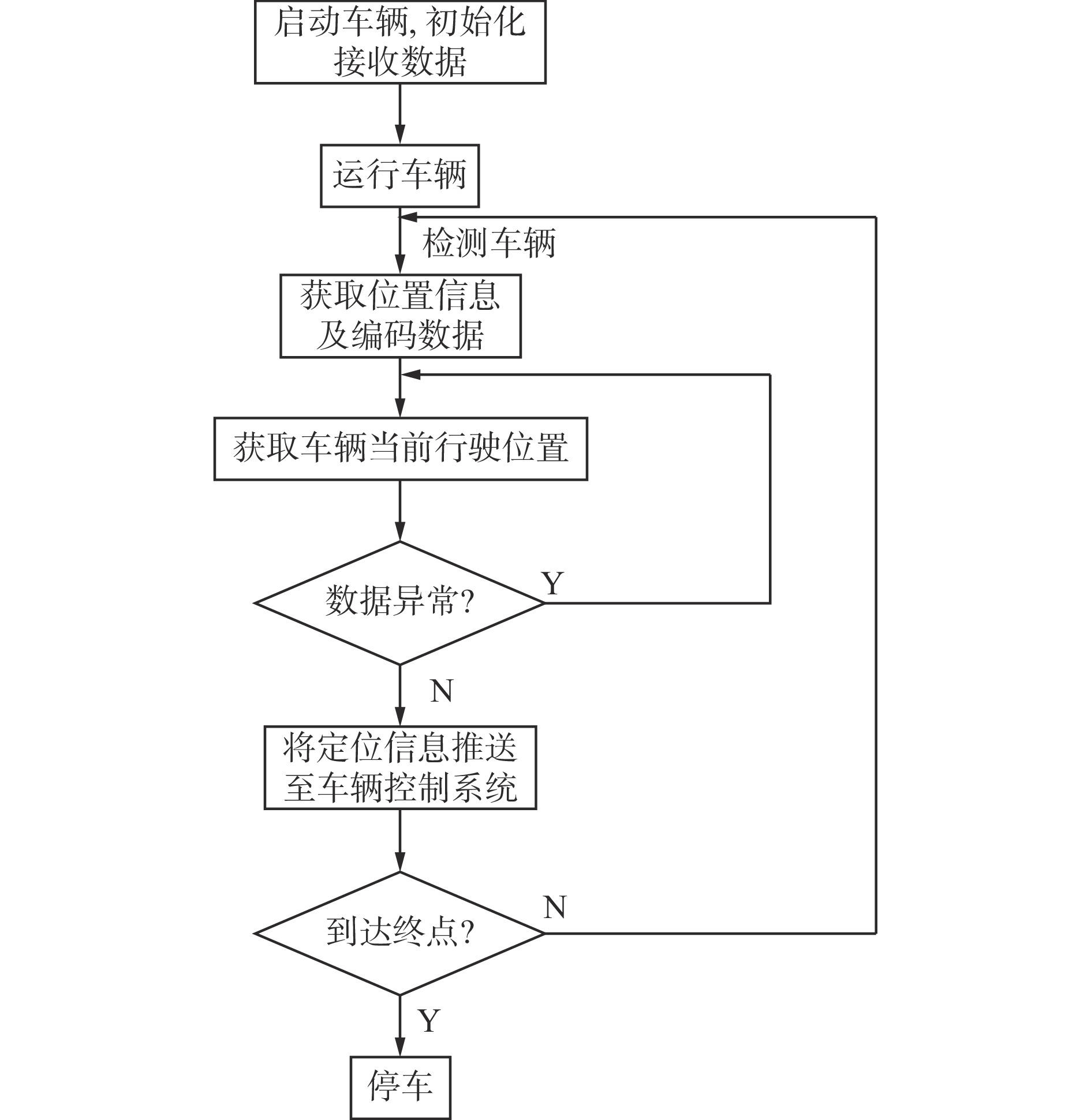
3. 磁寻迹定位试验
磁寻迹定位技术在实际应用时,磁钉需在磁感应天线的检测范围内才能被检测到。在车辆以正常速度行驶情况下,对磁钉能否在磁感应天线有效范围内及时产生感应脉冲信号,磁感应天线能否有效捕捉到该感应脉冲信号等方面进行研究。在响应时间为50 ms的情况下,对磁钉响应速度进行了试验研究。当磁感应天线经过编号为2080的磁钉时,在主感应区间电导率达700 μS/cm,说明只要在磁感应天线范围内布置磁感应强度大小合适的磁钉,磁感应天线可有效捕捉磁钉脉冲信号,电导率越高磁感应天线就越容易捕获磁钉的脉冲信号,磁感应天线获取磁钉脉冲信号的响应速度也就越快。
在单个磁钉满足磁感应天线检测响应时间(50 ms)的前提下,在车辆行驶线路上布置编号为1632,2049 2颗磁感应强度大小不同的磁钉,且在安装在车辆上的磁感应天线距地面约30 cm的状况下进行井下车辆行驶速度为40 km/h的模拟试验。当磁感应天线经过编号为1632的磁钉时,1632号磁钉能产生350 μS/cm电导率信号,当磁感应天线经过编号为2049的磁钉时,2049号磁钉能产生650 μS/cm电导率信号,磁感应天线均能有效捕捉获取磁钉脉冲信号,说明磁感应强度大小不同的磁钉会产生不同的电导率,磁钉磁感应强度过小产生的电导率低、产生的脉冲信号弱,磁感应天线捕获脉冲信号的难度增大,但磁钉磁感应强度过大会导致磁钉成本增加,磁感应强度过大的磁钉导致现场安装难度加大,因此通过设计合理的磁感应强度磁钉,得到合理的电导率,以保证磁感应天线有效捕捉脉冲信号,并达到降低成本易于安装的效果。
4. 磁寻迹定位关键技术
4.1 磁钉及磁感应天线设计
结合目前矿用车辆行驶速度最高为40 km/h的实际情况,将磁感应天线布置在车辆前方,将磁钉嵌入在巷道地面以下,这样既能满足磁感应强度和磁钉防护的需求,又不影响车辆正常行驶。
研究并开发了适用于煤矿自动驾驶带编号的无源感应磁钉,其外观为黑色圆柱形,高度为50 mm,直径为10 mm,具备防尘防水功能。无源感应磁钉安装于巷道地面以下,磁钉上端部距地面5 mm,在无源感应磁钉与磁感应天线无障碍物遮挡情况下信号发射范围为300~500 mm。
研究并开发了煤矿自动驾驶用磁感应天线,其外形尺寸为600 mm×250 mm×120 mm(长×宽×高),有效读取范围为500 mm×175 mm,IP等级为65,磁感应天线经过无源感应磁钉的速度为3 m/s,定位精度为±5 mm,整体重量为10 kg。磁寻迹定位精度受磁感应天线磁场生成周期影响,即磁场发生的频率越高,定位周期越短,获得定位精度也就越高。在磁感应天线和无源感应磁钉数据通信响应时间固定的情况下,定位精度主要受车辆行驶速度影响,车辆行驶速度越快,磁感应天线和无源感应磁钉的相对移动速度就越快,获得定位精度就越低。
当磁感应天线直接安装在金属上,易受强电磁干扰的影响,因此在使用过程中应在磁感应天线周围300 mm内,特别是在外壳周围没有强电磁干扰。为避免与煤矿现有系统频段产生接收信号冲突,磁感应天线选用64±4 kHz的频段,以避免其他信号的干扰。通过加大磁感应天线体积的方式提高磁感应天线检测可靠性。磁感应天线在自动驾驶车辆正前方通过支架连接布置,磁感应天线通过连接车辆电源进行供电,通过CAN总线与自动驾驶系统进行通信。经测试,当2根磁感应天线之间的距离为100 mm时,总电压波动降低达±5%~?15%,2根磁感应天线之间的距离小于200 mm时,总电压最高波动降低6%,将会影响测量结果。根据车辆结构、硬件要求、车辆定位系统需求及现场条件,确定磁感应天线具体安装位置:2根磁感应天线之间距离应大于200 mm,但磁感应天线距地面应不大于20 cm。将磁感应天线安装于车辆前部,既保证了磁感应天线与无源感应磁钉的距离和无障碍物遮挡的要求,又解决了车辆抖动易造成精度波动大的问题,提高了磁寻迹定位的稳定性。
4.2 磁寻迹定位算法
通过磁感应的方式获取车辆位置信息,采用批通知树(Batch Informed Tree,BIT*)算法对定位路线和轨迹进行计算,并根据车辆定位信息选择自动驾驶路径,磁寻迹路径搜索过程如图3所示。首先,在可通行空间内进行磁钉原有布置位置采样,采样点包括起点和目标点。其次,根据X_samples?X_free函数计算方法从起点 x_start 开始建立空间树结构,该空间树将从起点 x_start 开始不断向终点 x_goal 进行搜索,直到搜索到目标点或该树再无法拓展为止,即确定了最终路线。再次,根据起点 x_start 和终点 x_goal 的相对关系缩小搜索域,剔除不在新搜索域内的磁感应点,在缩小后的搜索域内重新寻迹采样磁钉,更新空间树节点的父子关系,根据迭代的结果缩小搜索域,在计算过程中不断重复上述迭代和计算过程,直至路径收敛至最优,停止迭代计算,至此完成寻迹路径的搜索过程。最后,对搜索结果进行平滑处理即得到最终结果,车辆按照计算结果,根据最优路径按轨迹行驶。
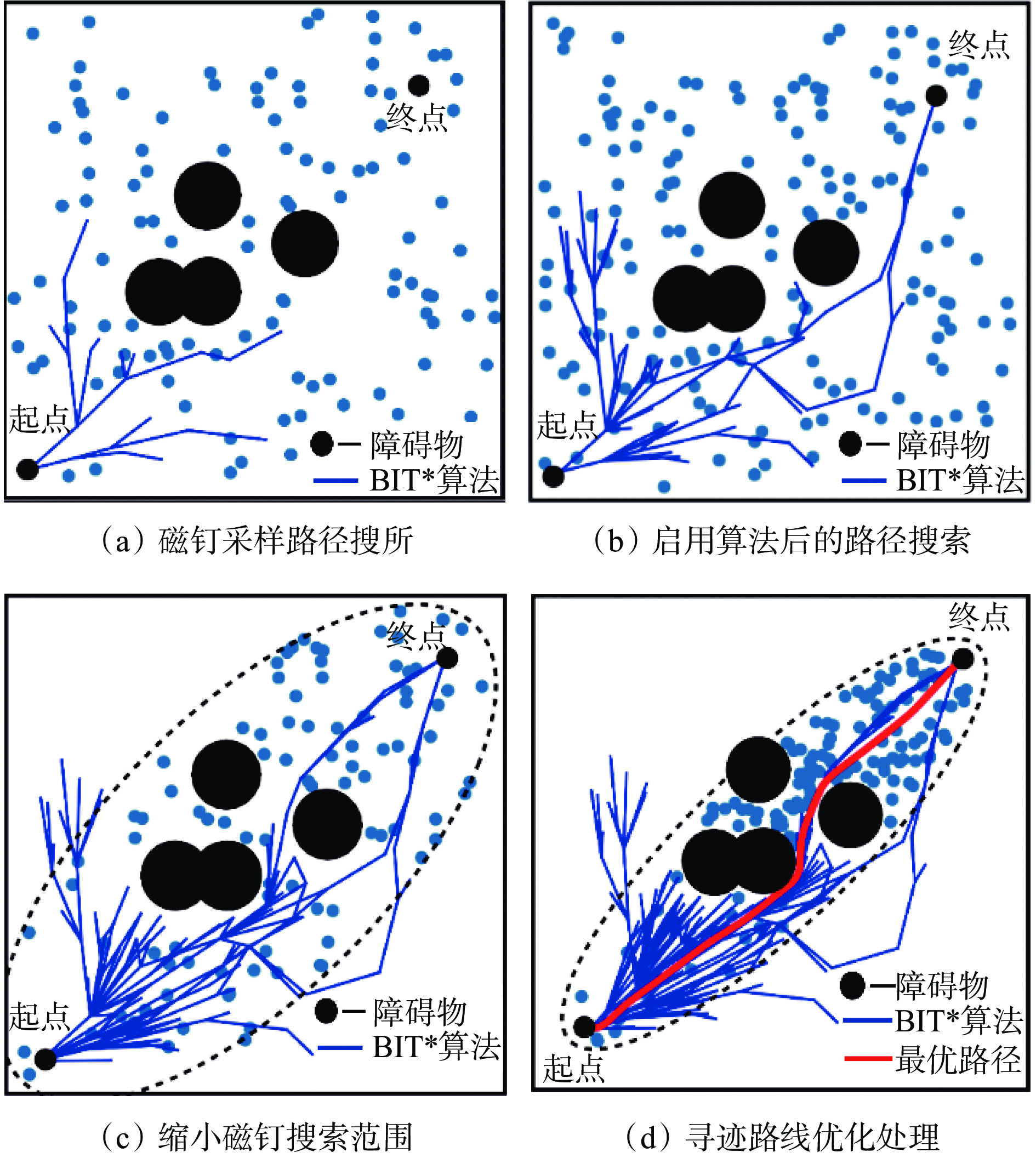
5. 现场应用
5.1 磁钉布置方案
结合陕煤集团神木张家峁煤矿的巷道实际情况进行方案设计,无源感应磁钉具体布置如图4所示。常规路段采用单排等间距布置无源感应磁钉。辅助运输车辆从地面进入井口时,GPS定位信号消失,因此,在距井口20 m左右重点布置无源感应磁钉。由于在巷道转弯处自动驾驶对测量精度要求提高,在巷道弯道前后6 m处重点布置无源感应磁钉。在车辆行驶路线的终点前后30 m处重点部置无源感应磁钉。在井口、弯道和车辆行驶路线的终点重点布置场景处,采用5排4磁钉和2排5磁钉相结合的方案布置无源感应磁钉。4磁钉布置方式具体分2排,每排与巷道中心线交错排布,一个磁钉距巷道中心线24 cm,另一个磁钉距巷道中心线72 cm,2排间距为52 cm。5磁钉布置方式具体为2排,第1排3磁钉,第2排2磁钉,且与巷道中心线对称,距离分别为96,48 cm,前后两排间距为52 cm,既满足自动驾驶响应速度、定位精度、低延时的需求,又满足不妨碍矿上生产且经济性最优的效果。
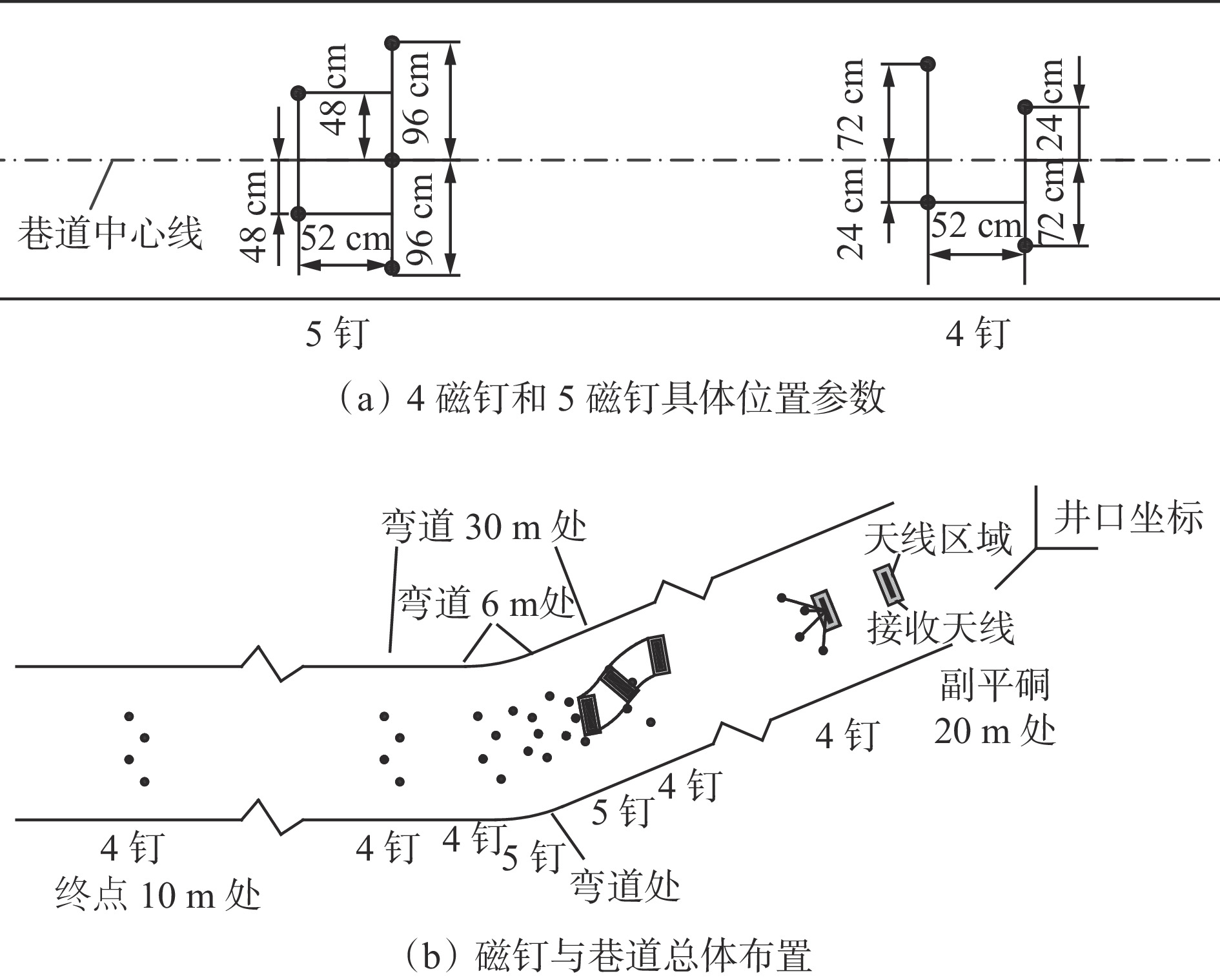
5.2 应用效果
在张家峁煤矿进行了工业性试验,在实施过程中,磁感应天线安装在燃油料车车头部位,无源感应磁钉与磁感应天线之间无障碍物或金属干扰,磁感应天线在自动驾驶车辆上抖动不明显,保证磁感应天线的稳定性。
在自动驾驶车辆行驶的巷道中心线预先布置带有编号的无源感应磁钉,然后将无源感应磁钉相对于巷道中心线的坐标转换为自动驾驶统一坐标。自动驾驶车辆按照正常程序启动,给磁感应天线等装置上电,自动驾驶车辆开始正常行驶,当自动驾驶车辆进入巷道时,车辆定位系统由GPS定位自动切换至磁寻迹定位,此时自动驾驶车辆经过无源感应磁钉并接收脉冲信号,车辆控制系统根据BIT*算法计算出车辆所在巷道的相对位置,达到定位寻迹的目的。如磁感应天线的数据异常,则会再次重新获取数据,直至数据正常。若自动驾驶车辆行驶路线有所偏差,自动驾驶车辆控制系统将对车辆方向、速度进行调整,更正车辆行驶路径。通过磁寻迹定位技术实现了自动驾驶车辆毫米级高精度、毫秒级低延时、有效的寻迹定位,使自动驾驶车辆按照最优路径准确行驶至终点。
6. 结论
(1) 设计了符合煤矿环境的无源感应磁钉和磁感应天线,在行驶的巷道中布置数个带有编号的无源感应磁钉,在具备辅助运输自动驾驶车辆车头下部安装磁感应天线,通过CAN总线通信方式与自动驾驶车辆通信,磁感应天线通过获取无源感应磁钉脉冲信号,经过数据处理和算法计算出车辆和无源感应磁钉的相对位置,从而得到车辆目前行驶的实时位置,通过BIT*算法实现寻迹路线的规划计算,并将计算结果发送至车辆控制系统,实现矿用车辆自动驾驶的寻迹定位。
(2) 矿用自动驾驶车辆行驶过程是个复杂的运行场景,自动驾驶需对固定障碍物、其他移动物、岔路等综合分析考虑,需通过激光雷达、毫米雷达波、红外测距等多种方式实现自动驾驶,不能单纯依靠磁寻迹定位一种方式,通过多传感器融合判断实现对随机障碍物等的判断分析,通过车辆控制系统实现自动避障或停车避让。后续在磁感应天线感应范围、结构体积优化等方面需进一步提升优化,为煤矿辅助运输车辆自动驾驶提供一种定位技术保障。
来源:工矿自动化